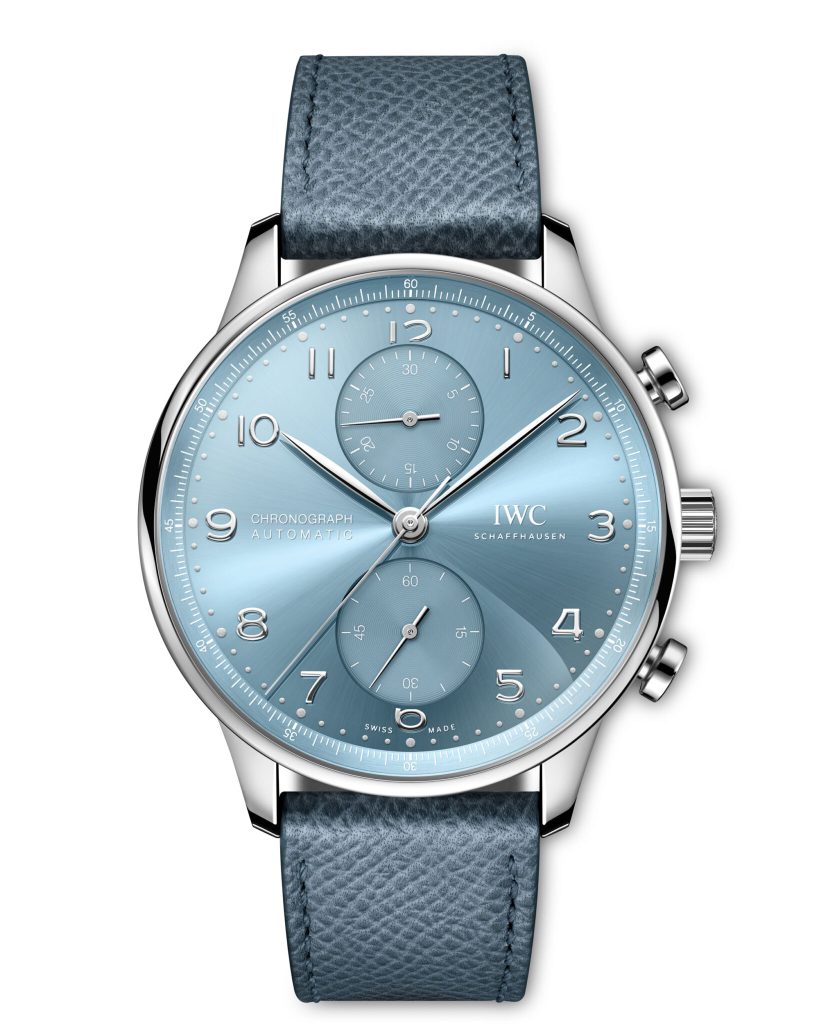
Das komplett schwarze Uhrengehäuse. Ein Symbol für Modernität, Tarnung, Sie wissen schon … Taktik. Ein Gegenstück zu den Jahrhunderten luxuriös glänzender Edelmetalle. Ok, vielleicht übertreibe ich ein bisschen, aber es ist unbestreitbar, dass schwarze Uhrengehäuse und die komplett schwarze Ästhetik bei Uhren durch die zyklische Natur von Uhrentrends ihr Durchhaltevermögen bewiesen haben.
Wo haben wir den Beginn dieser Entwicklung im Uhrenbereich gesehen? Nun, während viele Materialinnovationen in der Uhrmacherei eher technischen Wünschen entstammen, scheint das Konzept der komplett schwarzen Uhr aus einer rein ästhetischen Perspektive entstanden zu sein und in den 1970er Jahren stark aufzukommen.
Enicar und Porsche Design
Die meisten Quellen scheinen das erste schwarze Uhrengehäuse dem Porsche Design Chronograph 1 zuzuschreiben, der aus dem Kopf des legendären Ferdinand Porsche stammt. Jeff Stein von OnTheDash scheint jedoch anderer Meinung zu sein, wie er in seinem Hodinkee-Artikel von 2021 über die Heuer Black-Coated Monaco schrieb. Vor der ikonischen Einführung des Chronographen 1 im Jahr 1972 schien Enicar der Marke einige Jahre voraus gewesen zu sein, als sie Ende der 60er Jahre den Enicar Sherpa OPS vorstellten.
Schneller Vorlauf in die Gegenwart. Wir sehen viele weitere Fertigungstechniken und Materialien, die es Marken ermöglichen, dunkle Uhrengehäuse zu vielen verschiedenen Preisen und aus vielen verschiedenen Gründen herzustellen. Heute werden wir uns die drei wichtigsten Methoden ansehen, die eine Beschichtung oder Oberflächenbehandlung irgendeiner Art beinhalten, um ein schwarzes Finish zu erzielen. Bleiben Sie dran für Teil zwei, in dem wir uns feste Materialien in diesem Bereich ansehen.
Physikalische Gasphasenabscheidung (PVD)
Physikalische Gasphasenabscheidung ist wohl die gängigste Methode in der Branche, um ein schwarzes Gehäuse zu erzielen. Es ist ein weit gefasster Begriff, der mehrere spezifischere Techniken umfasst, aber in diesem Fall werden wir uns auf die gängigste Version für Uhren konzentrieren – die Lichtbogenionenplattierung.
In eine Vakuumkammer geben Sie sowohl die Beschichtungsverbindung (oft Zirkonium oder Titannitrid) in ihrem festen Zustand als auch das Uhrengehäuse. Nachdem die Kammer aufgeheizt wurde, werden Energiebögen in die Beschichtungsmasse entladen. Dadurch verdampft die Masse in der Kammer und bildet ein Plasma, das die Beschichtungselemente positiv auflädt.
Anschließend wird eine negative Spannung in das Uhrengehäuse geladen. Da die in der Vakuumkammer umherfliegenden Beschichtungspartikel positiv geladen sind, werden die Beschichtungspartikel von der negativ geladenen Oberfläche des Gehäuses angezogen und setzen sich zu einer dünnen und gleichmäßig verteilten Beschichtung ab. Nach dem Abkühlen – voilà! Sie haben ein schwarzes Gehäuse!
Im Zusammenhang mit der Behandlung von Uhrengehäusen müssen wir Haltbarkeit und Härte besprechen. Als Referenz hat 316L-Stahl eine Härte von etwa 150 HV auf der Vickers-Skala. Wenn man sich die Websites vieler PVD-Lieferanten ansieht, sieht es so aus, als ob viele gängige PVD-Behandlungen 2500–2800 HV ergeben. Aus Haltbarkeitssicht ist PVD von den drei Behandlungen, die wir heute untersuchen, die am wenigsten haltbare. Meiner persönlichen Erfahrung nach zeigten viele der schwarz PVD-beschichteten Uhren, die ich besaß, nach weniger als einem Jahr Abnutzungserscheinungen. Das ist Teil des Charmes, aber für diejenigen, die vom Zustand ihrer Uhren besessen sind, ist PVD vielleicht nicht die richtige Wahl. Trotzdem kann PVD aufgrund der geringeren Produktionskosten sehr begehrenswert sein. Sie finden PVD-beschichtete Stahluhren im Einstiegsbereich von Marken wie Timex und Swatch, wodurch viele erschwingliche Uhren ein schwarzes Finish erhalten.
Die Produktionsmethoden scheinen sich in den letzten Jahren verbessert zu haben, um die Produktion großer Stückzahlen zu bewältigen, was neben höherer Konsistenz und Qualität sicherlich auch zu überschaubareren Kosten führen wird. „Bei meinen letzten Besuchen bei Herstellern war ich begeistert, dass neue Technologien implementiert wurden, um das Volumen und die Konsistenz der Produktion und Ergebnisse zu verwalten“, sagt Jonathan Ferrer, Designer und Gründer von Brew Watch Co. Er erläutert die zahlreichen Schritte, die erforderlich sind, um Teile wie Uhrengehäuse vorzubereiten, bevor sie überhaupt in die Vakuumkammer kommen, um eine Beschichtung zu erhalten. „Eine zeitaufwändige Herausforderung bestand darin, jedes einzelne Bauteil [manuell] auf Bauteilbäume zu legen“, ein Drahtgestell, das die verschiedenen Teile in der Vakuumkammer hält. Jetzt, sagt Jonathan, sind die Prozesse vollständig automatisiert, was Faktoren wie Geschwindigkeit und Genauigkeit in einer sterilen Umgebung verbessert.
Ein weiterer kürzlich verbesserter Prozess ist das Maskieren – das Abdecken von Teilen eines Bauteils, die während des Prozesses nicht beschichtet werden sollen. Anstelle des mühsamen manuellen Prozesses von früher „scannen Maschinen jetzt Uhrenarmbänder und -gehäuse und spritzen eine Silikonlösung ein, die die Teile vor der Beschichtung/Veredelung abdeckt“, sagt Ferrer, anstatt dass ein Arbeiter winzige Abschnitte einzeln nacheinander abklebt.
Diamantähnlicher Kohlenstoff (DLC)
Was ist also der Unterschied zwischen DLC und PVD? Wenn man sich schwarz beschichtete Uhren ansieht, sind dies normalerweise die beiden Oberflächen, die besprochen werden. Oft hört man, dass DLC „besser“ ist. Technisch gesehen sind das keine gleichen Begriffe. DLC ist ein Beschichtungsmaterial, aber es kann auch physikalische Gasphasenabscheidung als Auftragungsverfahren verwenden. Es steht für „diamantähnlicher Kohlenstoff“ und das bedeutet, dass die betreffende Beschichtungsverbindung hauptsächlich aus Kohlenstoffatomen besteht.
Wenn Sie an den Chemieunterricht in der Schule zurückdenken, werden Sie sich daran erinnern, dass unterschiedliche kristalline Strukturen von Kohlenstoff sehr strukturell unterschiedliche Ergebnisse liefern können, obwohl sie aus denselben Kohlenstoffatomen bestehen. Die kristalline Struktur von Graphit ist geschichtet, was es weich macht. Diese einzelnen Schichten aus Kohlenstoffatomen haben keine starken Bindungen zueinander, sodass die einzelnen Schichten abrutschen können – denken Sie an Bleistift und Papier. Bei Diamanten sind die Kohlenstoffatome jedoch sehr dicht zusammengepackt und jedes Atom ist mit den anderen um es herum verbunden, was zu extremer Härte und Haltbarkeit führt.
Stellen Sie sich „diamantähnlichen Kohlenstoff“ als ein Zwischending vor – das die nützlichen Eigenschaften beider Strukturen aus der Perspektive eines Beschichtungsmaterials nutzt. Während die reinste Form von DLC aus rein sp³-gebundenen Kohlenstoffatomen (der Diamantart) bestehen kann, werden Sie bei einer kosmetischen Oberflächenbehandlung von Uhren höchstwahrscheinlich auch sp²-gebundene Kohlenstoffatome (die Graphitart) in der Mischung sehen. Auf diese Weise erreichen Sie sowohl Härte als auch einen niedrigeren Reibungskoeffizienten. In Kombination führen diese Eigenschaften zu einer strapazierfähigeren Oberfläche.
Mit DLC erhalten Sie etwas, das extrem schwer zu zerkratzen ist und je nach Anteil der Kohlenstoffmischung von mattem Anthrazit bis zu tief glänzendem Schwarz reichen kann. Auf den Websites einiger Anbieter können DLC-Beschichtungen üblicherweise eine Härte von 5000–9000 HV aufweisen. Zum Vergleich: Ein Diamant hat auf der Vickers-Skala eine Härte von 10000 HV.
Der Hauptgrund sind die Kosten. Ich habe mich an Giovanni Moro gewandt, einen der Mitbegründer von Unimatic, da die in Mailand ansässige Marke DLC-Beschichtungen seit ihren Anfängen in ihre Designsprache integriert hat. Giovanni erinnert sich, dass sie den Black-Out-Trend schon früh faszinierend fanden – er hatte sogar darüber nachgedacht, seine persönliche Omega Speedmaster mit einer Beschichtung zu versehen. Obwohl die verbesserte Härte, die mit DLC einhergeht, wünschenswert war, weist er darauf hin, dass die Kosten im Vergleich zu einer gleich hochwertigen Oberfläche mit Standard-PVD-Verbindungen manchmal bis zu 350 % höher sein können. Trotzdem bleibt die Marke bei der Verwendung von DLC für alle ihre Produkte mit schwarzem Gehäuse.
Keramisiertes Titan
Zu guter Letzt gibt es noch eine weitere Oberflächenbehandlung für Uhrengehäuse, die heutzutage verwendet wird: keramisiertes Titan. Theoretisch vereint es die großartigen Eigenschaften beider Materialien in seinem Namen – Sie erhalten die hohe Kratzfestigkeit von Keramik, während die strukturelle Integrität von Titan erhalten bleibt.
Am beliebtesten ist das markenrechtlich geschützte Ceratanium von IWC, das auf einigen ihrer Modelle aus dem Jahr 2017 zu sehen ist, als sie es auf dem Aquatimer Perpetual Calendar erstmals einsetzten. Was es jedoch auszeichnet, ist, dass keramisiertes Titan (nicht unbedingt) eine Beschichtung ist – und sich auch nicht auf das Grundmaterial bezieht. Etwas verwirrend? Lassen Sie es mich erklären.
Bei DLC und PVD wird eine separate Verbindung ionisiert und dann am Uhrengehäuse haften. Bei einem Material wie Ceratanium von IWC gibt es jedoch überhaupt keine separate Verbindung. Vielmehr beginnt man mit einem vollständig gefrästen Uhrengehäuse aus Titan – IWC verwendet seine proprietäre Legierung, auf die wir gleich zurückkommen werden. Sobald das Gehäuse (und andere Teile wie Kronen, Drücker und Schnallen) für die Behandlung bereit sind, kommen sie in einen Ofen. Diese Teile werden dann bei hoher Hitze gebrannt, und hier findet die Alchemie statt. IWC nennt das, was als nächstes passiert, eine „Phasentransformation [bei der] die Oberfläche des Metalls keramisiert wird“. Durch diesen Schritt erhalten diese Teile eine sehr gleichmäßige, mattschwarze Farbe. Ok, das klingt schick. Aber was passiert hier eigentlich?
Dieses 2002 eingereichte US-Patent scheint einen Blick hinter die Kulissen zu gewähren, da es ein Verfahren beschreibt, das dem von IWC verwendeten ähnelt. In dem Patent gibt der Erfinder Edward Rosenberg an, dass das „Verfahren zur Herstellung eines metallischen Gegenstands mit einer schwarzen Zieroberfläche“ eine Legierung erfordert, die „zwischen etwa 51 und 70 Gewichtsprozent Titan, zwischen etwa 3 und etwa 17 Gewichtsprozent Niob und den Rest aus einem Metall aus der Gruppe bestehend aus Zirkonium, Tantal, Molybdän, Hafniumzirkonium, Chrom und Mischungen davon“ besteht. Ich gehe davon aus, dass eine Kombination dieser Metalle die proprietäre Legierung ausmacht, die IWC derzeit verwendet, aber das kann niemand mit Sicherheit sagen.
Während des Erhitzungsprozesses beginnen einige der Metalle in der Legierung in der sauerstoffreichen Umgebung des Ofens zu oxidieren. Dabei wächst im Wesentlichen eine keramische Kruste aus der Legierung, wodurch das Titan keramisiert wird. Durch die Art des Prozesses wird diese Kruste im Vergleich zu jedem anderen Verfahren der Dampfabscheidung viel widerstandsfähiger gegen die Ablösung von der darunterliegenden, nicht oxidierten Titanlegierung. Wenn wir uns PVD als die rote Wachshülle um einen Babybel-Käse vorstellen, ist diese Keramisierung wie eine Kruste, die sich auf einem schönen Sauerteig bildet.
Ich sprach mit meinem Freund Ryan Norbauer, Hersteller luxuriöser mechanischer Tastaturen und Allround-Material-Nerd, über Ceratanium. Er erwähnte, dass er eine ähnliche Oberfläche für seine Tastaturen untersuchte, bei der ein Verfahren namens Mikrolichtbogenoxidation zum Einsatz kam, um eine sehr haltbare und optisch gleichmäßige Keramikschicht auf einer Aluminiumtastatur zu bilden, sodass die Oberfläche nicht auf die gleiche Weise abgenutzt würde wie bei PVD. Die Mikrolichtbogenoxidation, die häufig für Unterhaltungselektronik verwendet wird, erzielt ein ähnliches Ergebnis wie das Verfahren von Ceratanium, jedoch mit leicht unterschiedlichen Methoden. Anstelle einer Wärmebehandlung ist dieses Verfahren elektrochemisch und beinhaltet das Schießen von Lichtbögen auf ein in ein alkalisches Bad getauchtes Metall. Angesichts dieser Unterschiede ist Edward Rosenbergs Patent bemerkenswert, weil es „ohne den Einsatz von Chemikalien, Elektrolyten, Elektrizität oder komplexen Wärmebehandlungsgeräten auskommt“. Ironischerweise wird das, was wir im Uhrenbereich als modernes Material betrachten, angeblich auf eine bewusst einfachere und primitivere Weise hergestellt.
Wie hart ist Ceratanium also? IWC veröffentlicht die Härte des Materials nicht öffentlich, aber man kann mit Sicherheit sagen, dass es im Vergleich zu PVD beispielsweise deutlich kratzfester ist, da die äußere Schicht, die sich bildet, buchstäblich aus Keramik besteht. Überall im Internet habe ich ein paar Leute sagen hören, ihr Ceratanium sei zerkratzt – obwohl Kratzer auf Keramik oder Keramikschichten oft tatsächlich von dem Metall des anderen Objekts herrühren können, das auf das Gehäuse übertragen wird, das schließlich entfernt werden kann. Es scheint, dass der Hauptschuldige Federstegwerkzeuge waren, obwohl ich neugierig wäre, ein Foto von jemandem zu sehen, der wirklich durch die Keramikschicht gekratzt hat. Ich denke, nur die Zeit wird zeigen, ob die aktuelle Generation der Ceratanium-Uhren unseren Erwartungen entspricht, aber derzeit scheint es sich um mehr als nur eine Marketingübung zu handeln, sondern um ein wirklich einzigartiges Material in der Uhrmacherei mit greifbaren Vorteilen.
Wenn Sie an diesem Artikel interessiert sind, hat unsere Website diese Replica uhren